Toyota Kirloskar Auto Parts Pvt Ltd (TKAP) brought in productivity improvement in the transmission machining line through in-house low-cost automation. Other advantages followed, justifying the much-needed change.
Project triggers
Factors that influenced the project include (refer Image 2)
Internal – Increasing cost competitiveness among affiliates and year-over-year rise in labor costs.
External – Fluctuating market conditions (Government regulations), shifts in customer demands (hybrid/electric vehicles), and intense competition.
At Toyota, our approach is to ‘increase value-added work and reduce supplementary and non-value-added work’, effectively utilizing manpower. However, in practical scenarios, most manpower is consumed for non-value-added tasks, particularly in the parts conveyance system.
As the project progressed, we noticed that dedicated manpower was being utilized to transport raw materials/parts
in bins from the warehouse to the manufacturing line using tow motors and manual dollies, leading to conveyance muda (waste of transportation) and operator fatigue.
A study was conducted to implement automation solutions, tailored to our specific requirements, aimed at enhancing productivity (reducing manpower and investment, in alignment with our objectives).
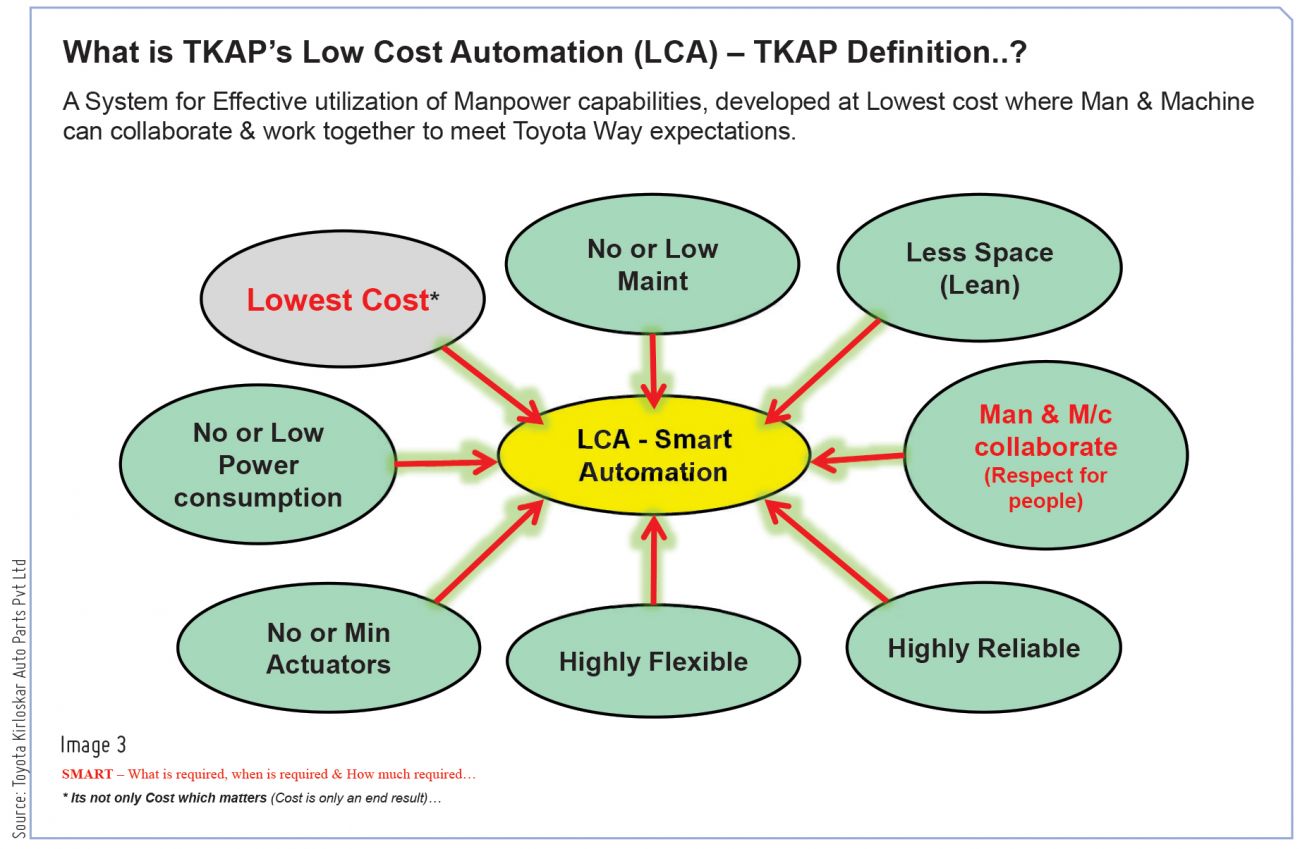
The decision was made to utilize in-house resources and their expertise and experience to develop an LCA (Local Conveyance Automation)project to meet the target (TKAP’s LCA tools).
|
Key concerns
- Implementing general automation not only presents cost-related challenges in terms of Return On Investment (ROI), but also has difficulties in terms of safety, environmental impact, flexibility, and lead time.
- Kaizens need to be incorporated from the project’s inception to realize the benefits from the very first day of line off.
- Demonstrating cost competitiveness with other affiliates is crucial, as there is always competition to secure the project. This has, therefore, triggered a parts conveyance automation project to enhance productivity and reduce manpower.
Solution generation, innovation and complexity
Initially, various outsourced measures were evaluated to meet the target.
- Automated overhead conveyors: These had limitations such as high cost, longer lead times, and extensive space coverage. They offered limited flexibility for future modifications and alsoincurred high maintenance costs.
- Outsourced high-capacity AGVs: They too proved to be a costly option and also required annual maintenance contracts (AMC) and additional conveyor automation.
Therefore, the decision was made to utilize in-house resources and their expertise and experience to develop a LCA (Local Conveyance Automation) project to meet the target (TKAP’s LCA tools) (refer Image 3).
Finally, the in-house team proposed a concept to develop a high-capacity AGV with the capacity of towing raw materials/parts (weighing 1,000 Kg) supplied in bins from the warehouse to the manufacturing line without human intervention. The proposal was presented to management and with their approval and support, the innovative development of high-capacity AGV commenced.
TKAP had previously gained experience in-house by developing low-capacity AGVs (ranging from 100 to 500 Kg) for parts conveyance. Although the journey of in-house AGV development posed challenges and initially consumed time, we took up the challenge of creating a more capable high-capacity AGV to be more cost-competitive and enhance productivity, with considerable potential for expansion.
However, the more challenging part was yet to come as the proposed development of AGV will only serve the purpose of towing the dolly from one location to another location. The key challenge was also to develop a solution to automatically load and unload the parts from AGV dolly to manufacturing line side conveyors (the proposed concept of line side conveyors was automated and equipped with powered motors and chain drive) and eliminate any manual interventions.
To meet this automatic load and unload requirements on AGV, the team technically proposed to use Toyota’s Karakuri technique to develop low-powered Karakuri pushers using a rope and pulley mechanism (image 4). A proto was developed initially
to build confidence and evaluate the needs. The same was showcased and a consensus was built with related stakeholders (MFG, MNT, PC) to reflect on PDCA.
The developed proto gave us much more confidence in proposing to convert the line-side powered chain conveyors to free roller-based Karakuri chutes using a similar rope and pulley concept, thereby further simplifying the solutions, reducing the investments, and achieving the targets with lesser lead time (minimum bought out parts were used).
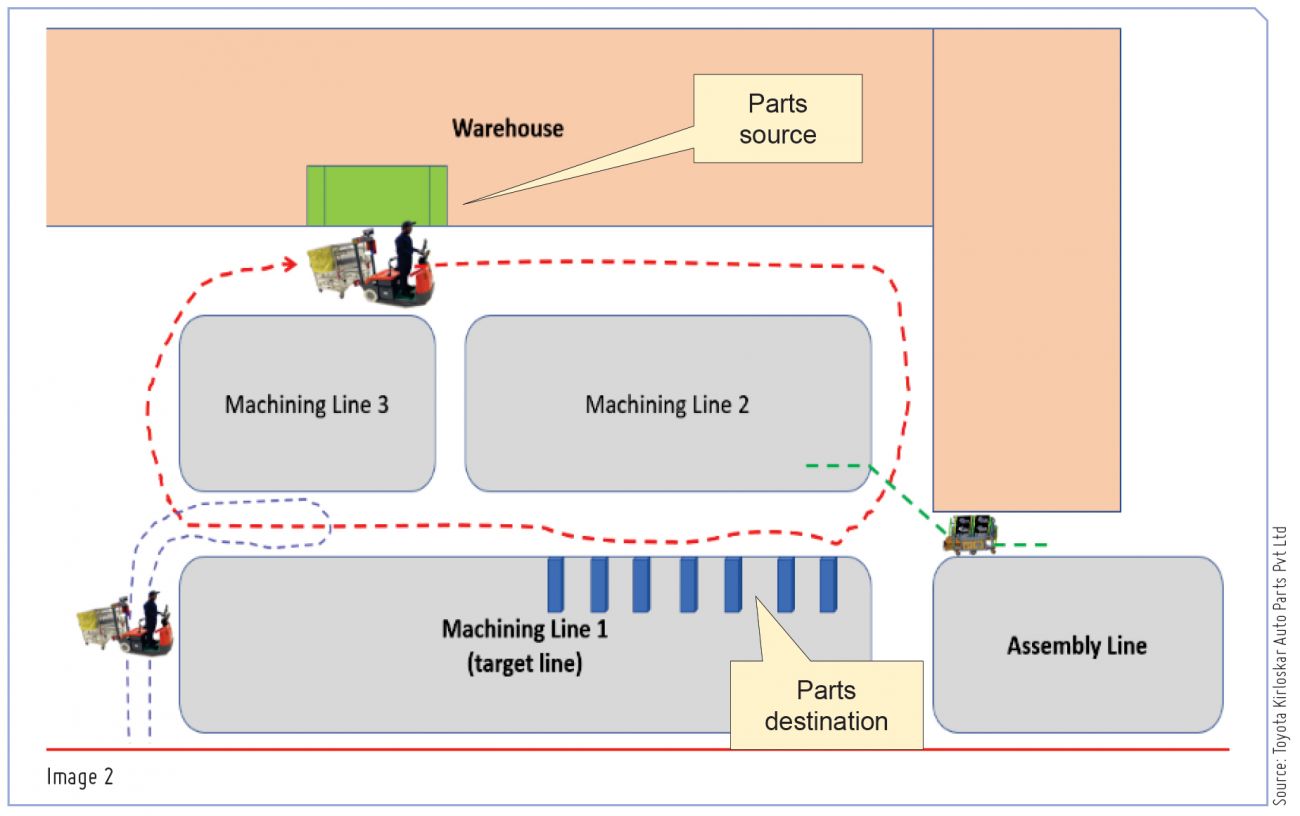
To meet automatic load and unload requirements on AGV, the team technically proposed to use Toyota’s Karakuri technique to develop lowpowered Karakuri pushers using a rope and pulley mechanism.
|
Innovative solutions developed
- High-capacity AGV: The developed high-capacity AGV was modular with the ease of interchangeability and the ease of backup. It had a bidirectional movement and a higher capacity battery to cater to the full load for 2 shift operations. It was also Wifi-equipped to control traffic and communication with line side Karakuri chutes.
- Free rollers conveyors with Karakuri drive: The Karakuri pushers have a rope and a pulley. The auto slip concept is for pusher return movement. The pushers help in the flow of full and empty bins in double-deckers. Auto loading of empty bins onto AGV is enabled with an extended Karakuri pusher arm. These auto slip pushers detect overloads. Accumulation conveyors are enabled with Karakuri technology.
- Intelligent part delivery concept: Memory logic enables delivery locations with types of parts plus variants. QR code read ensures accurate stopping. Chute and AGV wireless communication enables load/unload status checks. The system works on a need-based approach.
- Traffic management: Traffic lights are used to control AGV and other vehicle traffic control. Priority-based signaling is used for AGV and other AGV traffic control.
Key challenges and countermeasures taken
There were several challenges involved, including:
- Ensuring the safety features of AGV: We did not want to compromise on safety and, hence, resorted to measures such as implementing primary safety scanners for obstacle detection, incorporating secondary bumper stoppers, and also having two stoppers in all chutes (primary and secondary, per Toyota spec).
- High-capacity drives & battery backup for AGV: This challenge was addressed by setting technical parameters and specifications to meet targets, implementing an engineering approach to calculate the drive and battery capacity, and lastly, sourcing drive motors and batteries locally.
- Backup in case of AGV failure (first-time attempt): For which a modular AGV design was introduced that allowed for extraction out of the dolly and manual operation of it.
- Achieving AGV & dolly weight balance: This required using a tubular chassis with a metal plate body for AGV and a tubular frame structure for the dolly, equipping AGV with friction wheels and the dolly with ergonomic and heavy-load swivel wheels.
- Automatic parts transfer from AGV dolly to line conveyor & automatic receipt and feeding of parts in conveyor: This required implementing free roller conveyors with Karakuri pushers with rope and pulley and also auto slip pushers for reverse and overload movement.
- Interference with other lines leading to CT issues (long-distance travel): This was addressed by changing the warehouse layout to be closer to the manufacturing line by involving stakeholders and optimizing AGV routes to reduce travel distances.
- Balancing dolly to AGV length (where the length of dolly is significantly more than AGV: To tackle the above, the measure enabled modular AGV movement inside the dolly guide, ensuring that AGV was always ahead).
The batteries used in AGVs are Green Earth Batteries that cause the least harm to the environment and are also 100 percent safe in nature. Acid battery, considered harmful to nature in the case of leaks, has been eliminated.
|
Green impact
In line with the Toyota Environmental Challenge 2050, Eco kaizens achieved include:
The batteries used in AGVs are Green Earth Batteries that cause the least harm to the environment and are also 100 percent safe in nature. The use of the Tow Motor Lead Acid battery, considered harmful to nature in the case of leaks, has been eliminated. Karakuri drives in chutes consume less energy (1/3rd) than the conventional type motor, chain drives.
Result / Impact
- The shop floor’s overall safety has been enhanced: There was earlier the risk of collision between tow motors and humans, which has been eliminated. Man-dependent risk management, which was subject to change has been replaced by system-based risk management. Non-explosive batteries with BMS have been introduced that do away with the risk of battery explosion. High-torque actuators with direct drive have been replaced by low-torque actuators with a safety slippage concept.
- Quality in terms of the right part being at the right location has been ensured: There was human dependency and therefore, the risk of parts supply mix-up. Now because of the retentive memory logic in AGV, there cannot be parts supply mix-up.
- Green initiatives have been enhanced: Harmful Lead Acid batteries have been replaced by zero harmful green batteries. Also, now less energy gets consumed to charge batteries.
- Productivity gained: A reduction in headcount has been achieved.
- Delivery has been improved with on-time supply: The new system-based supply has led to zero dependency and, hence, no fluctuations. Travel time has also been optimized.
- Investment cost has been reduced: Earlier there would be costs such as tow motor and manpower costs. Now the AGV cost is less than the tow motor cost and also there is zero manpower.
- Running cost has been reduced: A significant reduction in the running cost has been achieved due to the transition from outsourced tow motor annual maintenance contracts (AMC) to in-house AGV maintenance, zero yearly manpower costs, and reduced AGV battery charging expenses due to lower capacity requirements.
- In-house skill levels have been enhanced (HRD): There has been a transition from low-capacity AGVs and high-skilled tow motor driver dependency to the development of high-capacity AGVs in-house. This shift has been complemented by training and knowledge transfer to the Manufacturing and Maintenance teams, eliminating dependency on high-skill levels and enhancing motivation through the reduction of ergonomic burdens associated with tasks such as pushing/pulling and loading/unloading heavy objects.
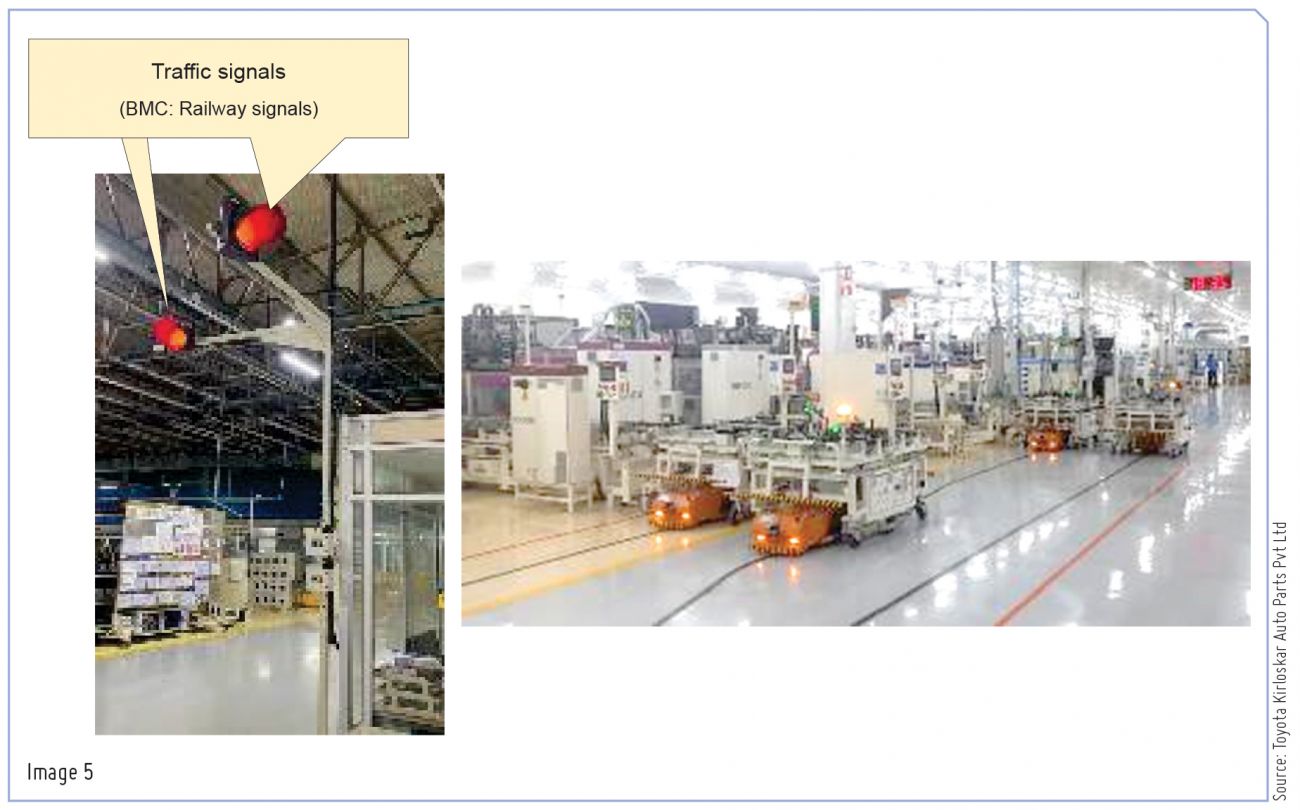
As we/Toyota India are upgrading our product line-up towards new technology like Hybrid and Electric vehicles, our production system also needs an upgrade from conventional to innovative solutions and automation.
|
Business sustainability
As we/Toyota India are upgrading our product line-up towards new technology like Hybrid and Electric vehicles, our production system also needs an upgrade from conventional to innovative solutions and automation, keeping in mind cost-competitiveness in the cost-sensitive Indian market. At Toyota India, we believe in growth through continuous improvement by adopting new technology for scale-up/expansion.
The below-mentioned TKAP’s AGV’s Roadmap and Karakuri Roadmap is a perfect example of continuous improvement through new developments and standardization for a scale-up.
- Skills of the in-house members were enhanced through the introduction of a new model
- The team was motivated to challenge themselves further with the next level of kaizens
- Deskilling was done by eliminating the dependency on highly skilled tow motor drivers
- TKAP’s self-reliance enhanced through the development of automation solutions
- Adapted to new technology in production systems, including hybrid and electric vehicles.
- Carbon footprint and CO2 emissions was reduced through automation
- Successfully secured 1 patent for innovation and uniqueness in the in-house developed ‘AGV Drive Mechanism’.
Business metrics
- TKAP production improvement through Karakuri and AGVs
- International Recognition for Karakuri: Achieved the ‘Global Best Idea Award’ for three consecutive times at the Japan JIPM Karakuri exhibition
- Reduction in new project investment achieved
- Proposed revenue generation model for AGVs: Successfully completed a trial sale of 1 unit.
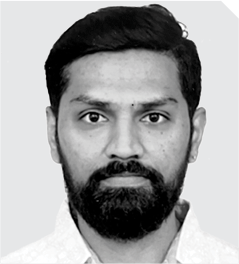 |
NIRANJAN MR
Manager
Toyota Kirloskar Auto Parts Pvt Ltd (TKAP) niranjan@tkap.co.in
|